Markem-Imaje, a global provider of marking and coding technologies and end-to-end supply chain solutions, is launching the industry’s most comprehensive range of digital, remote, and on-site hardware services to further improve customer uptime and productivity.
In October, Markem-Imaje will introduce a portfolio of after-sales service packages tailored to user needs and designed for Industry 4.0 environments. These services are created to minimize downtime, offering 24/7 remote support and customization options. As a global company, Markem-Imaje aims to provide customers with smart tools and easily accessible resources to maximize flexibility and productivity.
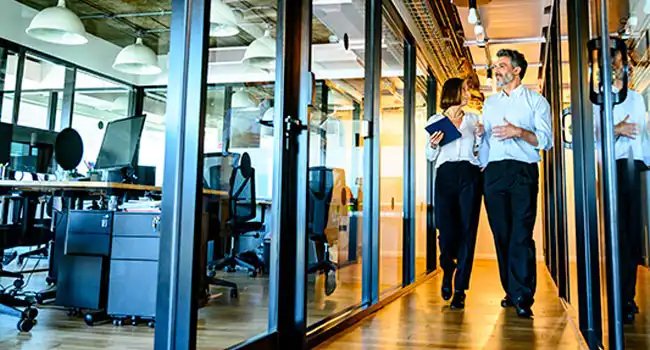

Digital services are a key part of this new offering, in line with industry demands. A survey by PMMI in January revealed that 55% of end-users prefer remote assistance to solve technical issues. The top three reasons for using remote support are reduced downtime, optimized production processes, and faster service. These elements are the foundation of Markem-Imaje’s commitment to innovation.
The new offering includes three levels of hardware maintenance services, with digital self-service options that allow line operators to resolve most issues themselves. This is a result of Markem-Imaje’s ongoing dedication to improving coding processes. Key features include a 24/7 AI-powered virtual assistant that reduces downtime by helping users troubleshoot on their own and offering a quick escalation process for more complex issues. Connected Printer services, based on secure IoT technology, simplify managing installed printers and ensure automatic process optimization, with real-time visibility and remote risk monitoring alerts available 24/7. Additionally, the online portal and shop allow customers to view their entire installed base, manage contracts, and order spare parts and consumables as needed.
The second service level is fully remote and includes live chat support available up to 24/7, instant remote assistance with live video guidance, and an expert help desk with access to local engineering and technical teams. This offer also includes the exclusive Markem-Imaje Advanced Exchange Service for quick and direct replacement of faulty parts.
For companies requiring on-site services and added security to reduce risks, Markem-Imaje offers services like preventive maintenance visits to avoid costly unplanned downtime, expert visits for advanced printer optimization, and on-site repairs performed by local service technicians. All maintenance packages can be customized to meet user needs, with different service levels depending on the required functionality.
“Our goal is to help customers maximize their uptime and get the best return on their investment in our hardware and software, no matter their size, industry segment, or location,” says Sean Cox, Global Services Director at Markem-Imaje. “It’s not just about having the right tools, but also about optimizing their use, and that’s what our tailored maintenance services aim to do. Much of our offering ensures near real-time support, addressing workforce skill gaps and eliminating the need for in-person interventions or waiting for assistance wherever possible.”
About Markem-Imaje
Markem-Imaje, a fully owned subsidiary of Dover Corporation, connects products and protects brands through intelligent identification, traceability, and consumer engagement solutions. We offer the industry’s most complete range of integrated marking and coding systems, along with reliable software, services, and consumables. More than 50,000 customers worldwide rely on us to unlock the power of the information within their codes.
With decades of proven experience and the world’s largest global network, we help our customers optimize supply chain efficiency, meet sustainability and compliance goals, ensure product safety, and engage consumers. Intelligence, beyond the mark.