Un briefing impegnativo, una ricerca meticolosa e un confronto tecnico ad ampia portata consulenziale. Si conclude il progetto di Cama per un “big boss” della torrefazione italiana. Le macchine sono in fase di installazione e le capsule pronte al decollo, per “lanciare” il Made in Italy di qualità in tutto il pianeta.
Nel B2B, supportare le necessità del cliente attraverso un’assistenza efficace è la chiave per sviluppare relazioni di fiducia durature. E se alcuni progetti si pongono fin da subito come percorribili, altri richiedono studi approfonditi, verifiche, aggiustamenti di rotta e dedizione. Proprio per questo, vengono definiti “sfidanti” e hanno la caratteristica di assicurare, quando conclusi, grandi soddisfazioni.

Per Cama, una delle sfide vinte e meglio concepite è quella in fase di compimento con un colosso italiano del caffè. Questo big player del settore si è rivolto all’azienda con l’obiettivo di sostituire le proprie capsule in polipropilene con soluzioni in alluminio 100% riciclato e disporre di un packaging ad altissima resa estetica e qualitativa, capace di sopportare i lunghi viaggi del prodotto dal nord dell’Italia nei cinque continenti. Il tutto, senza minimamente intaccare la qualità indiscussa del prodotto.
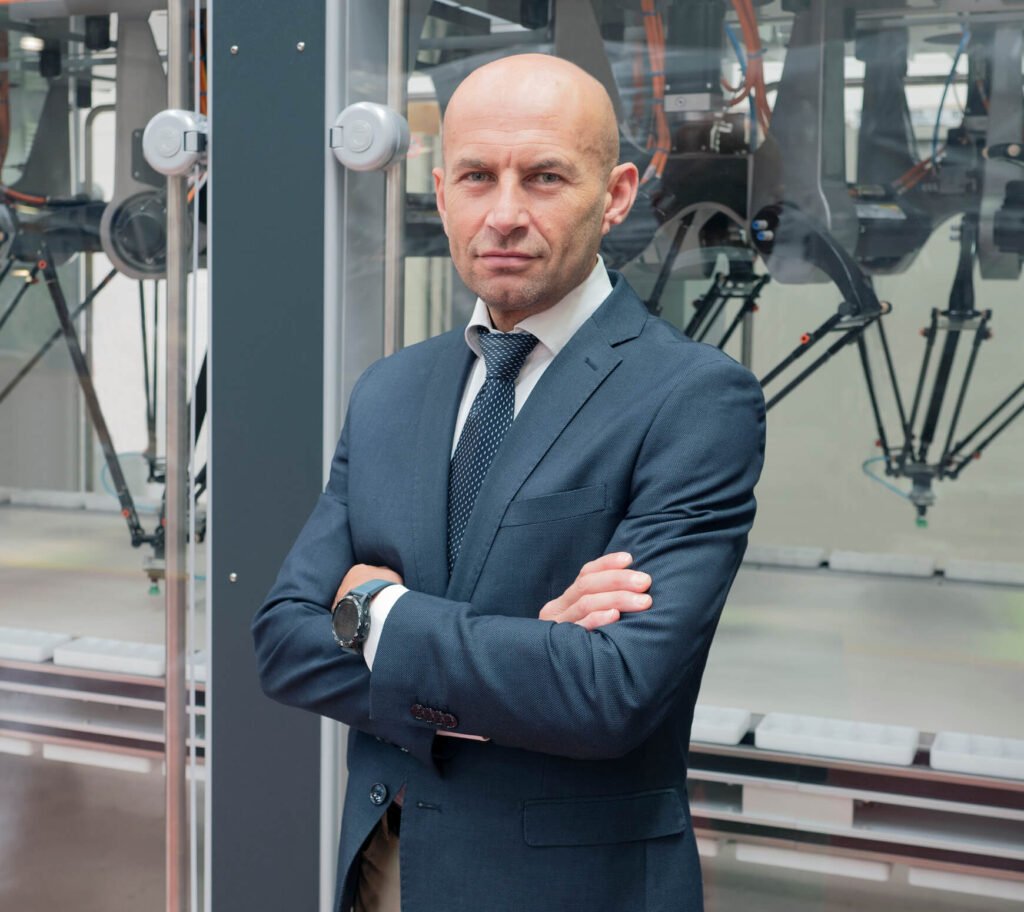
«Ci siamo mossi – spiega Sergio Cornago, Area Manager di Cama specializzato nel settore del caffè – in un ambito dalla qualità elevatissima, che ci ha visti partner del nostro cliente e che ci ha portati alla co-creazione del prodotto finale. Da briefing, le innovative capsule con gli opportuni adattatori, andavano meccanizzate in tutte le macchinette esistenti mantenendo la qualità del prodotto e il loro pack doveva garantire la massima protezione e superare i severissimi transport test aziendali.
Il nostro Reparto Packaging ha dato il meglio, assistendo il cliente da un punto di vista consulenziale e offrendo una risposta funzionale veramente molto interessante. Non solo abbiamo soddisfatto le richieste ma, grazie all’esclusivo risultato estetico, abbiamo anche regalato al consumatore finale un’experience unica già in fase di apertura della scatola, prima ancora che si diffonda l’aroma del caffè».
Nel dettaglio, gli astucci sono formati partendo da fustellato steso e sono in grado di mantenere le capsule separate tra di loro per preservare eventuali danneggiamenti durante il trasporto, tramite interfalde alveolari protettive, il tutto realizzato all’interno di una linea monoblocco.

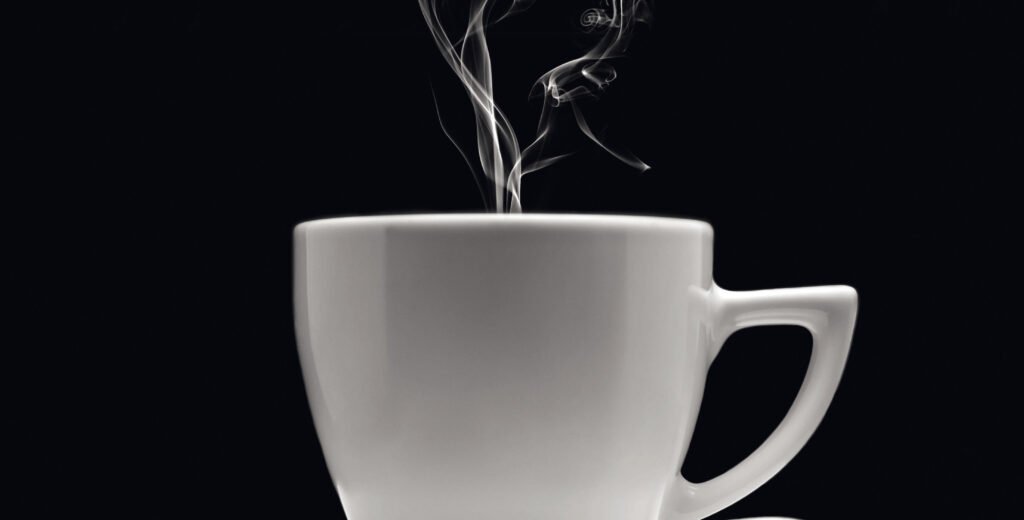
Il progetto è stato poi completato dalla Divisione System Engineering aziendale, che supporta i clienti nei progetti speciali e si è pertanto attivata per l’automazione del confezionamento. «Qui stava l’altra sfida – continua Cornago –, ossia modificare la macchina in dotazione, facendo in modo che questa potesse prendere i cartoncini, aprire il nuovo astuccio e procedere con il confezionamento. È proprio vero che quando ci si trova di fronte alla necessità di individuare una soluzione, le idee arrivano. Data la complessità del packaging, abbiamo previsto un sistema di pre-apertura dell’interfalda per proteggere e mantenere le capsule separate all’interno della confezione, integrando 10 robot smart e veloci.
Infine, abbiamo reso ogni modulo con due unità indipendenti che lavorano all’unisono ricevendo le capsule da 4 file. Questo a vantaggio della produttività che a richiesta può essere ridotta da 4 a 2 file, assicurando risparmio energetico e dà la possibilità di utilizzare l’altra metà della linea come back-up in caso di manutenzione».
Il progetto concepito per garantire la produzione di 850- 900 capsule al minuto ed è in fase di installazione presso il produttore di caffè. Una sfida complessa, superata con successo: il cliente è soddisfatto e Cama si riconferma partner ideale per trovare soluzioni capaci di combinare innovazione, tecnologia, sostenibilità e una buona dose di ingegno creativo.
