Achieving high-quality label application on a product with particularly challenging characteristics to manage: uneven surface, instability, soft surface and transparency. This was the goal of a leading company in cleaning, disinfection and hygiene solutions, looking for a system to apply a top label and a bottom label on refill packs of sanitizing gel.
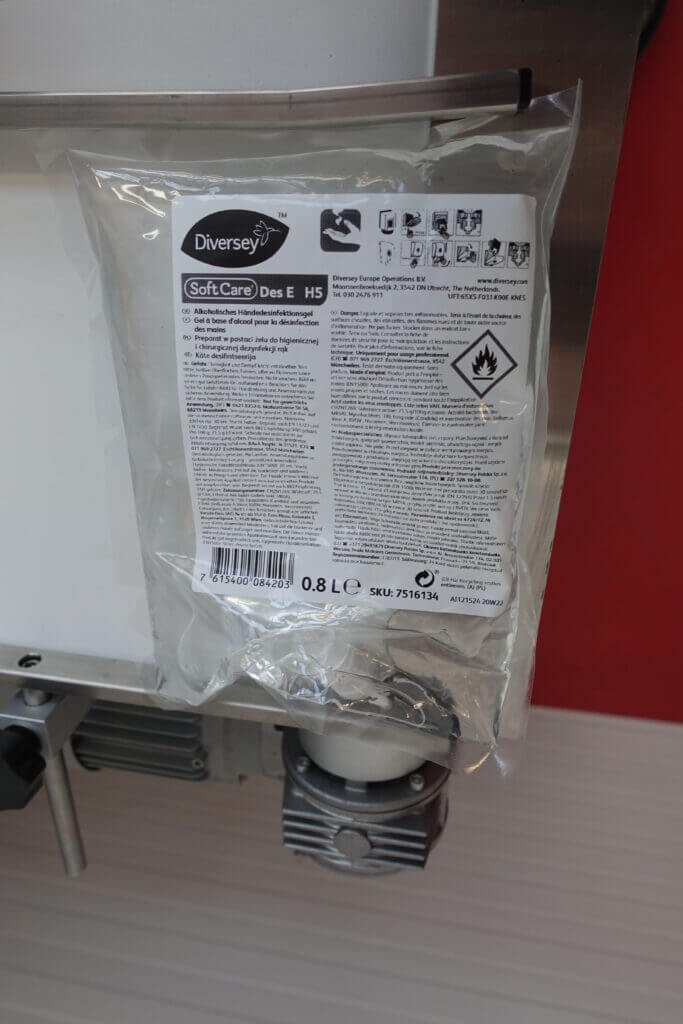
This challenge proved to be particularly exciting for Etipack, which was called upon to measure itself with the design of a system capable of allowing perfect labelling on such irregular packaging and of managing different label formats with precision and efficiency.
The solution: 4/2 customized system with two Strong 200 labellers and two print units for graphic layout and variable data.
In order to achieve the goal desired by the customer, Etipack has designed a special 4/2 System, allowing the application of labels in two formats, above and below the product, while at the same time, being able to print graphic data and variables on the surface of the labels before application.
System features and configurations
The system features two automatic variable data labeling and printing stations located at the bottom and top of an integrated product conveying system.
Two Strong 200 labelling machines with stepper motor, apply labels with an application speed of up to 20 m/min. They allow the recovery of backing paper up to 180 mm in diameter, thanks to the presence of a belt rewinder, and end-of-reel control thanks to an internal capacitive sensor.
The upper labeller is equipped with an adjustable long dispensing terminal for separating from the backing paper and applying a 20 x 40 mm sized label. The lower labeller incorporates a paper rotation unit for 90° orientation of a 140 x 120 mm sized label.
To allow precise and secure data printing on labels, the system integrates two industrial printing modules PEM 6” by Novexx Solutions equipped with “ribbon saving” mechanism and able to cover a printing width up to 160 mm with a 12 dots/mm (300 dpi) resolution.
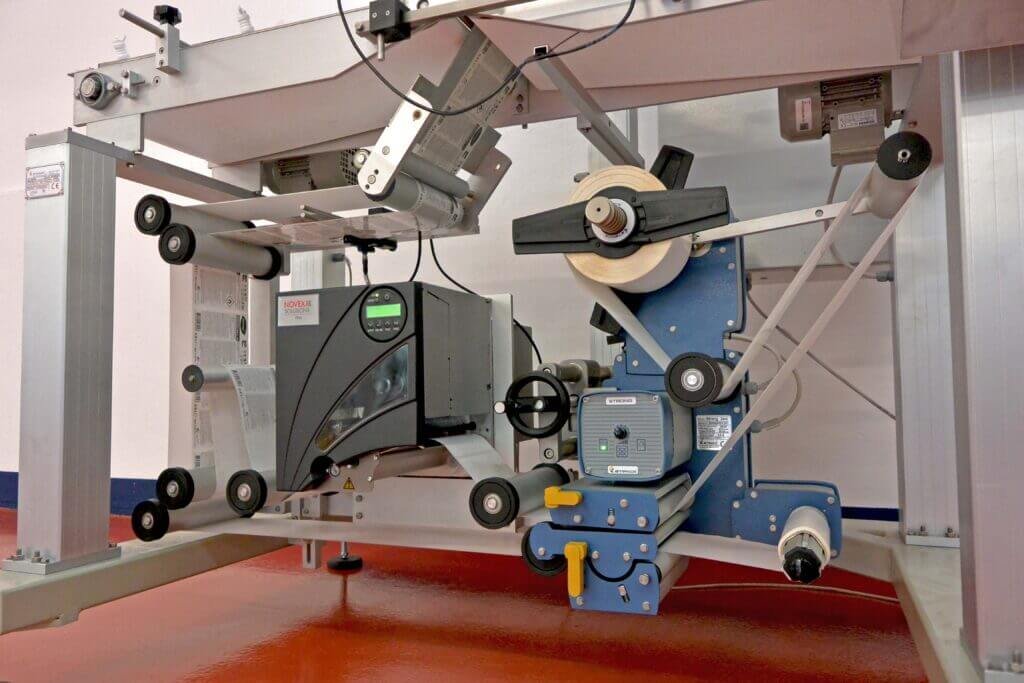

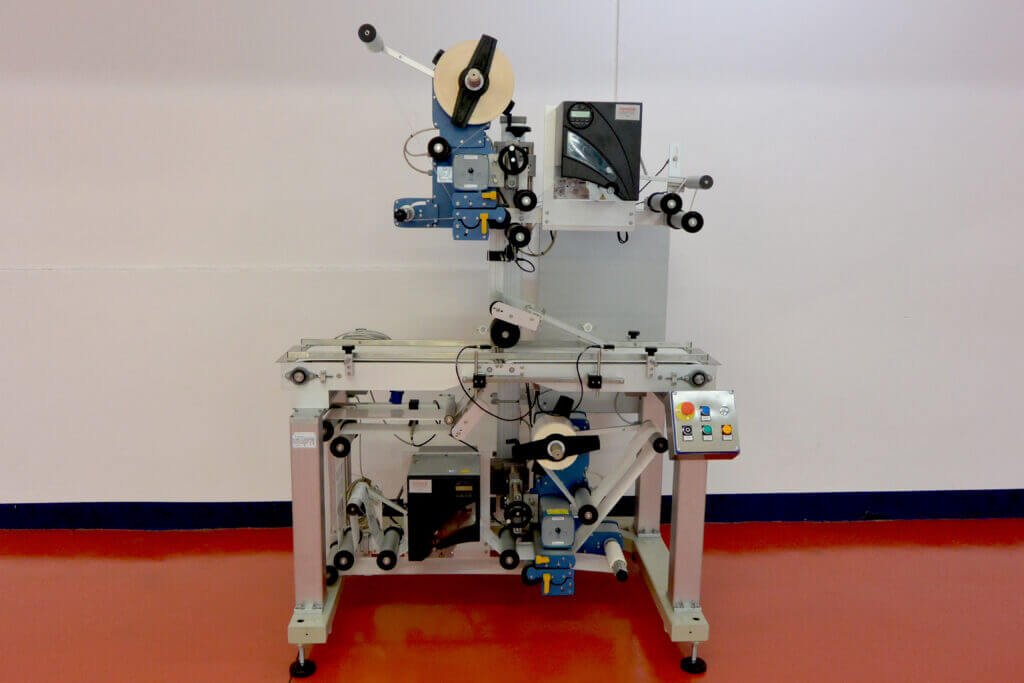
The printing unit located in the upper labelling station is dedicated to variable data overprinting on the smaller label. The printing unit located in the lower labelling station is programmed to print the graphic layout, together with variable data overprinting.
In order to obtain the perfect application on the particular package, the system uses two start photocells that allow the correct and reliable detection of the packaging by correctly managing the transparency, while a roller applicator acts on the irregular surface of the product by flattening it to facilitate the label application.
The system is included among the Sistema 4 series, which comprises a range of automatic labelling systems for the application of pressure-sensitive labels on the top and bottom of products. These systems are configured as small, self-sufficient labelling lines that transport and label the product, either offline or connected to other packaging machines such as filling and thermoforming machines.