According to Legambiente’s Beach Litter dossier (2019), at the top of the top 10 most commonly found wastes on Italian beaches are plastic and polystyrene pieces, which are the “precursors” to microplastics.
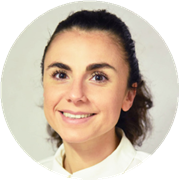
Silvia D’Alesio
In particular, beverage caps and lids (one per meter of beach), followed by cigarette butts, cotton swabs (7.4% of the total found), plastic bottles (45 every 100 meters), and plastic utensils (34 every 100 meters). This observation on waste and its dispersion highlights how single-use plastic for food products and related consumption practices represent a real and significant obstacle to environmental preservation.
Obviously, the problem is not limited to a single nation, so the recent European directive on single-use plastics addresses those wastes that are now among the most common on European territories. In fact, the (EU) 2019/904 directive on reducing the impact of certain plastic products on the environment introduces new measures and specific requirements to reduce the impact that food packaging continues to have on waste dispersed in the environment.
For example, beverage bottles and their caps are among the most common and polluting: caps can easily detach from their containers or be lost due to consumer distraction. For this reason, attention to packaging design remains high in the world of the food industry.
An event not to be missed, albeit now imminent, is Interpack: the fair held in Düsseldorf every 3 years, which brings together all the major players in the packaging industry. Exhibitors from around the world who operate in the Machinery, Equipment, Materials, and Services for Packaging & Packaging industry and supply various industries, including of course the food industry, will be hosted.
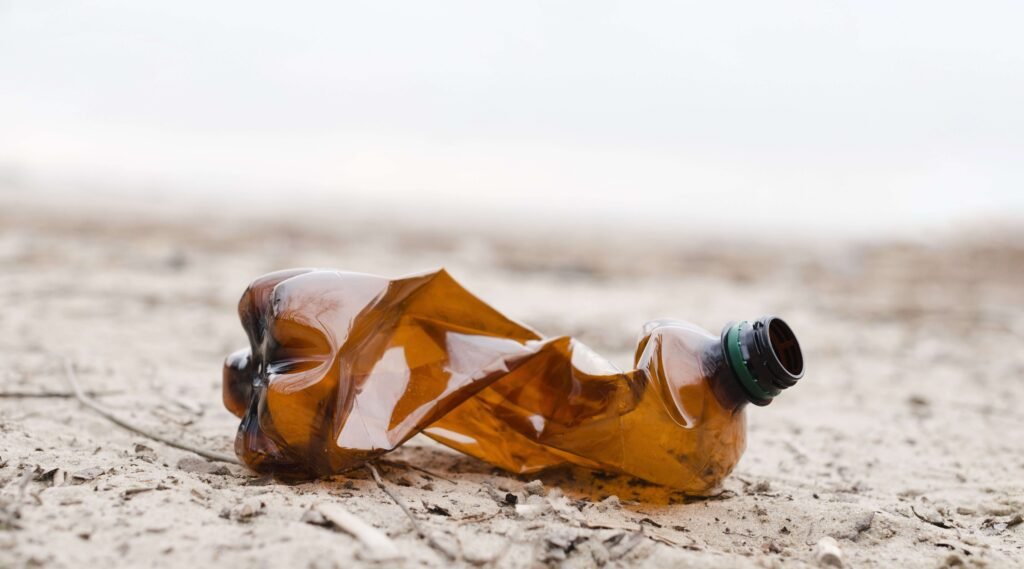
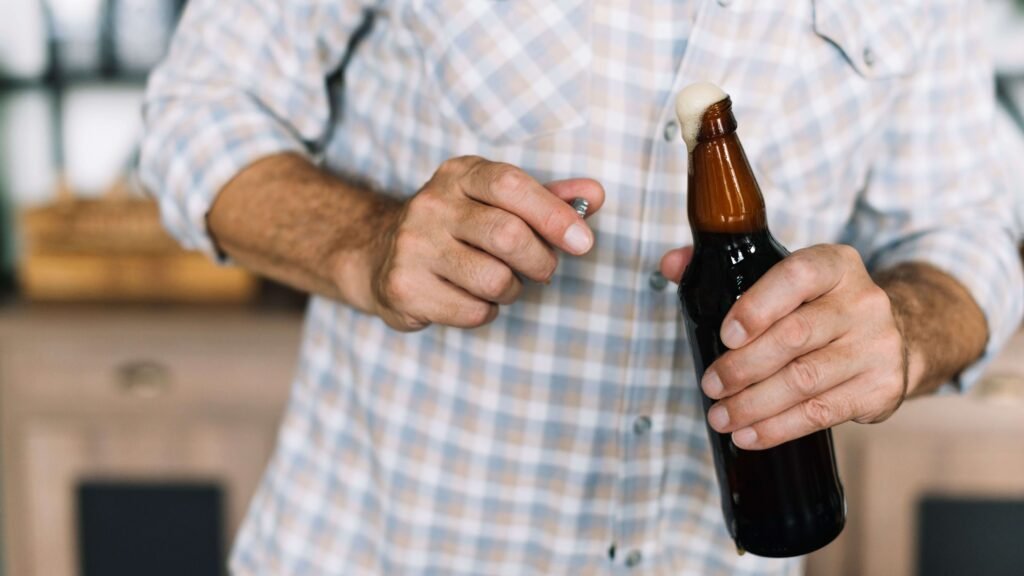
The day before the start of this major event, the hybrid PUMA conference organized by the Netherlands Packaging Centre (NVC) will also be held at the Sheraton Düsseldorf Airport Hotel: a significant event that aims to demonstrate the commitment of all stakeholders towards proposing new solutions in order to close a chapter of history that sees food packaging as the main cause of the global waste management problem.
Indeed, if we examine the evolution of food packaging, we can understand how it began in the 1800s when the food industry acquired the ability to preserve and transport food from production to consumption, preserving its quality. From preservation techniques such as the lyophilization of Russian chemist Dirchoff (1832) to the hermetic preservation of French pastry chef Nicolas Appert (1827), packaging was studied to solve difficulties in ensuring the quality of fresh food. Therefore, the holistic approach to innovation processes along food supply chains has always focused on optimizing the distribution and sales phase.
The PUMA conference offers a vast overview of all aspects related to the world of packaging and how they are interconnected. For example, if the intention is to spread a new process operation to agricultural producers, then how to design an effective ‘door-to-door’ solution?
Dr. Thatcher teaches the importance of never stopping in designing while paying attention to details. For example, observing the wide and smooth mouth of a bottle, calibrating its capacity based on consumption habits, its easy use and reuse, etc. His research included the closure system, starting the life of what we know as the spring cap or the integrated Milk Protector protection system. Therefore, particular attention should be paid to the design of closure caps and their materials (from metal to plastic) that respond to the different packaging and packaged food product requirements.
The evolution of patents related to the hermetic closure system follows the evolution of different packaging solutions and their requirements (in the example of the bottle, whether to give it a cylindrical shape, a wide body, or a wide mouth, etc.).
In the 1900s, other containers that needed to be sealed and other materials or formats (such as W.L. Wright’s waxed paper bottle, conical or square in shape (1918)) allowed for the improvement of the hermetic closure system.
The succession of these packaging solutions accelerated the shift from traditional solutions, such as the example previously mentioned of glass bottles used for over 40 years to distribute foods such as milk, oil, and even water (in Paper bottles newest type of sanitary milk: dispensing means, now being substituted for glass, Science & Invention Magazine, 1929), thus testifying to the link that has always united innovation and design processes (in food packaging, for example, production and process costs associated with sanitary aspects are decisive) and pushing the market towards new solutions.
Over time, these solutions are increasing consumer awareness in an attempt to reduce their use of single-use items and increasing their commitment to environmental sustainability, etc.
However, it’s worth asking how marginal certain aspects of packaging design that respond to environmental needs are in the current scenario: how many packages are made from recycled materials, in new forms to reduce the amount of material used, with new gestures for a changing population, with new brands that offer consumers a more environmentally sustainable product image without misleading them with different information than that related to the product inside?
For this reason, it is important to continue to stay active (or rather, interactive) by participating in the debate on packaging as a driver of new production systems in the food industry that are truly sustainable. The opening and closing devices mentioned here are among the many lenses to use when observing these new solutions and then offering them to a market that is rightly more attentive to the planet’s needs. The cap is therefore a key element in continuing the more ecological metamorphosis of food containers.