In ever-increasing use, not only within the Pharmaceutical industry but also in the ophthalmic, cosmetic, and food industries for liquid packaging, Blow-Fill-Seal – BFS – technology is the highest standard of advanced aseptic production.
Challenges in Blow-Fill-Seal labelling are related both to the variety of formats available and, most importantly, to the shape of the packages, which can be stable or unstable. The term “stable formats” refers to packages, single or in strips, that have a flat surface allowing the product to be placed steadily on the labeling system conveyor belt.
On the other hand, the term “unstable products” refers to packages, single or in strips, that require support in order to be properly stabilized and transported, and which undergo horizontal processing.
Based on the listed features, Etipack can identify the most suitable label application method in relation to the labelling direction, namely, running parallel or perpendicular to the product placement.

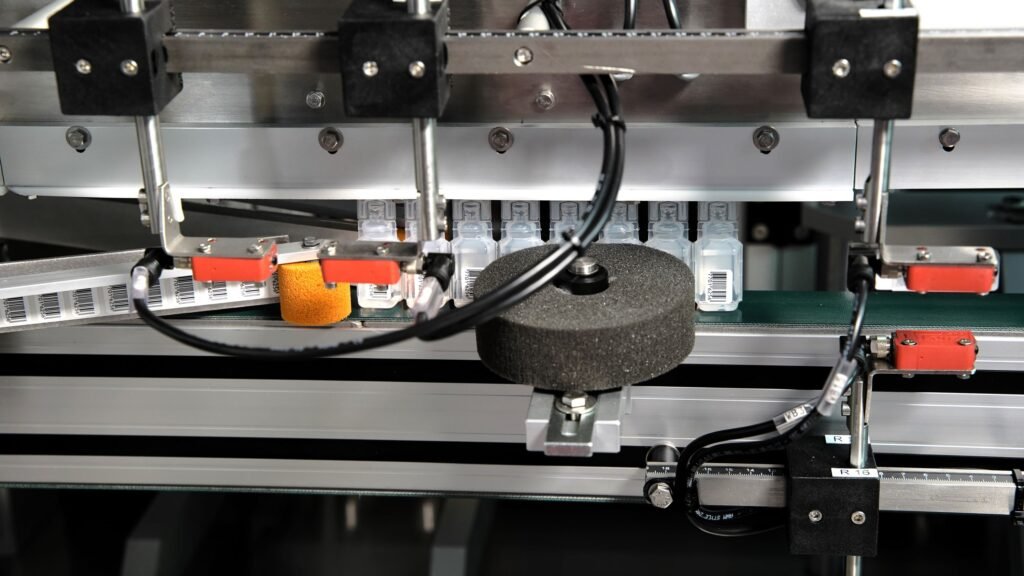
Etipack Blow-Fill-Seal application specific labelling systems
To ensure high-performance, customized labelling of different formats, Etipack has developed specific labelling machines for blow-fill-seal and singledose packages from thermoforming. These systems feature a high degree of integration with existing production and packaging lines and are distinguished by the type of products as well as the specific Pharmaceutical, Healthcare, and Cosmetics application needs.
3 solution examples to label various BFS formats that require different label applications
5/2 System for labelling unstable strips vertically
This particular System 5 is designed to transport 5 single-dose strips packs in an upright position, as well as apply double-sided labels to the body of products. It is equipped with a product stabilizing device (DSP) and a linear chain-orienting device to properly handle incoming products, along with a maximum load control system.
The presence of start photocells makes it possible to handle labelling on transparent products. For non-compliance product control, a system for rejecting unsuitable product is installed, with a failsafe photocell and control of good product at the exit. The System is fitted to integrate a vision system comprising two cameras to check on printing
4/2 System for labelling unstable strips horizontally
This System 4 is designed to be integrated into the line, handling packs of 5 single-dose strips in a horizontal position and applying a label over the body of the products. It is equipped with a special stabilizing device to condition the batches and features an incoming product locking system to hold the products coming in from the line while labeling.
The System is equipped with maximum load control, UV barrier labelling control photocell, failed product rejection system, and failsafe photocell ejection controls. It is also prepared for the integration of a printing unit including an OCV/OCR control camera.

System 3 for horizontal labeling of cylindrical vials with position shifting
This System is designed to handle cylindrical ophthalmic solution BFS vials in 3 sizes, as well as applying semiwrap labels. To accommodate products loaded in trays, the System integrates a rotating table that conveys the vials upright to the conveyor belt. To perform proper labelling, the system stabilizes the product by shifting it from a vertical to a horizontal position through the use of an auger. It then proceeds to apply the label, which, thanks to the presence of a DRP rotation device, gets properly wrapped on the bottles.
The System integrates a print unit for overprinting, an OCV/OCR print control unit, and a barcode reader located on the label dispensing blade. Label control is managed by two UV photocells. In addition, a product rejection system is also present featuring rejection control and good product exit control.
In order to handle Pharma-specific features, the System is equipped with Siemens PLC and ASEM Touch panel allowing CFR21 management, batch management including consultation and reporting, as well as back-up & restore and disaster recovery functions.
